Osmosis systems use osmotic membranes composed of thin sheets of semipermeable film that do not allow the passage of a series of substances depending on the size.
The membranes can be constructed in different ways, the one commonly used in primary water treatment is tube, for other applications flat capillary hollow fiber membranes are used, etc…
The industrial construction techniques of osmotic membranes can be by heat precipitation, high temperature sintering or film stretching. These are the main manufacturing procedures for membranes.
The materials normally used to make osmotic membranes are polysulfone, polyamines, cellulose acetate, polyethersulfone, polyacrylonitrile, the choice of material, and the type of construction, make an osmosis membrane with very precise characteristics and specifications based on polymer.
Other types of membranes are ceramic ones, these membranes are used in particularly aggressive environments, or with the need to operate at high temperatures.
Ceramic membranes are made with alumina, titanium oxides or zinc oxides, these materials give them a high stability and resistance.
The design of an osmosis plant must be supported by the analysis of the water to be treated and the results to be obtained, this allows to choose the level of automation, the necessary filtration pre-treatment, the most suitable osmotic membranes, the working pressure and the membrane cleaning systems integrated in the reverse osmosis plant.
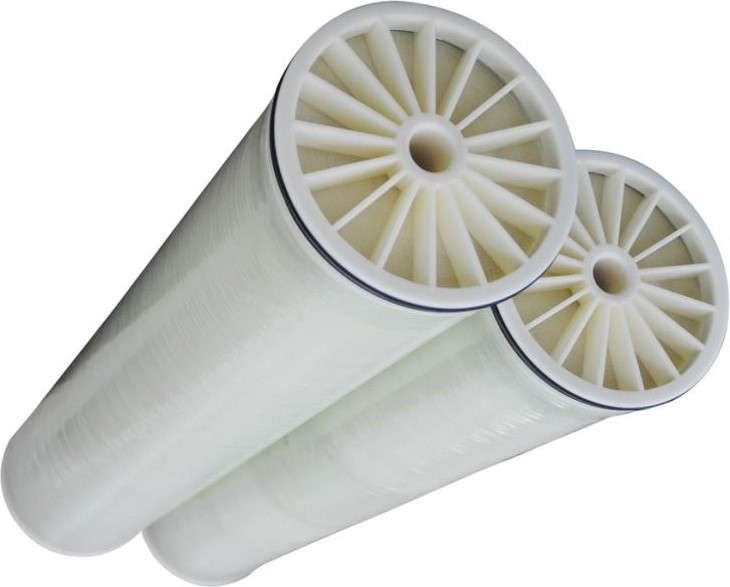